anatere, un spécialiste de la transformation de matière premières basé à Saignelégier, devait inaugurer fin septembre son premier «four solaire». Celui-ci doit permettre de fondre de l’acier recyclé AISI 316L nuance 4441 à partir de la seule énergie solaire, ce qui inscrit la société jurassienne en pionnière du mouvement «Circular Economy Switzerland».
Mais à la dernière minute, il y a eu un «couac», qui en a empêché l’ouverture. La procédure administrative pour l’implantation de ce four solaire révolutionnaire était bien avancée. Elle ouvrait aussi la possibilité de recours pour une éventuelle opposition. Un mois avant l’ouverture, prévue initialement pour le 27 septembre, une riveraine s’est manifestée pour interrompre le projet.
Raphaël Broye, PDG de Panatere, raconte: «Cela n’a en réalité rien à voir avec notre four solaire! Il s’agit plutôt d’une opposition à la ville. La riveraine n’avait pas pu faire les transformations qu’elle souhaitaiit sur son bâtiment, classé monument historique. Par son opposition à notre projet, elle a voulu marquer son agacement envers les procédures. Je lui ai parlé et elle ne reproche rien à l’implantation elle-même…» Une petite vengeance personnelle qui retardera le projet d’environ six mois – l’ouverture ne se fera donc pas avant le printemps 2023, avec les frimas de l’hiver qui sont en train arriver.
Le site du futur concentrateur solaire (c’est de cela qu’il s’agit réellement) se déploie à 1’000 mètres d’altitude pour assurer un ensoleillement de première qualité. Raphaël Broye se veut rassurant: «Les travaux de génie civil ont bien avancé. Les autorités locales nous ont bien aidés pour accélérer la procédure de levée du blocage et la riveraine n’a pas souhaité faire un nouveau recours. L’autorisation est bel et bien accordée.»
-
- Raphaël Broye, fondateur de Panatere
Essais parallèles en Suisse, France et Tunisie
Où en est Panatere dans la mise en place de ce four? «Sur le site suisse, nous avançons au plus vite avant les premières chutes de neige, répond le directeur. Simultanément, des tests grandeur nature sont en cours dans la région de Kairouan en Tunisie (désert du nord du pays, ndlr). C’est un site sur lequel l’EPFL travaille historiquement, car l’intensité lumineuse y est excellente. En Suisse, nous avons évalué plusieurs endroits pour notre infrastructure. L’idéal serait à 2’500 mètres d’altitude pour un soleil optimal, mais la logistique d’approvisionnement et de livraison deviendrait plus compliquée. Sierre, où l’ensoleillement est maximal, était aussi une option, mais notre site actuel est le plus proche de la source des déchets d’acier en plein Arc Jurassien. Nous avons privilégié le circuit court au maximum.»
Les premiers tests de la technologie du concentrateur solaire, ceux du four solaire d’Odeillo, ont été menés à Mont-Louis, près de Perpignan en France, en collaboration avec le CNRS. L’application n’était que semi-industrielle. «La configuration de notre machine nous place dans une phase d’industrialisation véritable, précise Raphaël Broye. Seuls 57 fours solaires à concentration sont en service dans le monde et ils sont essentiellement destinés à la recherche et au transfert de technologies, par exemple pour tester la résistance à très haute température du nez de la fusée Ariane ou celle des freins à disque en F1.»
«Seuls 57 fours solaires à concentration sont en service dans le monde et ils sont essentiellement destinés à la recherche et au transfert de technologies.»
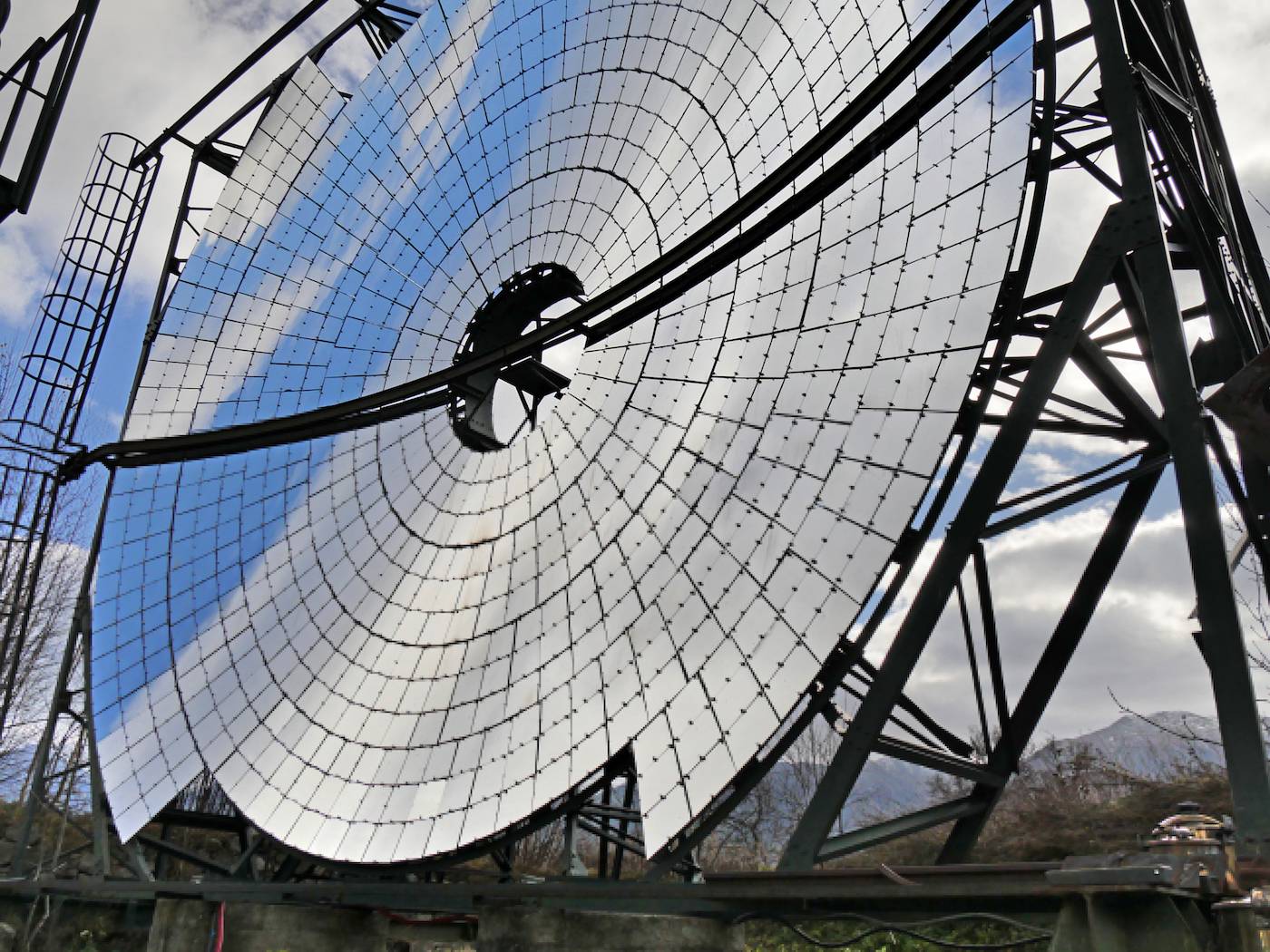
Couvrir les besoins en acier de toute l’industrie?
Pourquoi n’y a-t-il pas eu d’applications industrielles jusqu’à présent? «Certaines existent dans l’automobile, mais encore aucune en micro-technique, poursuit le responsable. Avec ce premier four, nous pourrons produire 100 tonnes d’acier recyclé de cette manière. Cela représente de quoi équiper 6 millions de montres… mais seulement 14 minutes de production pour un gros fondeur, d’où le peu d’intérêt démontré par ces derniers.»
Pour mettre ces chiffres en perspective, 15,7 millions de montres ont été produites en Suisse en 2021 (source FH), dont 62% en acier, soit moins de 10 millions de pièces. La fonte de l’acier récupéré localement, via un four solaire, permettrait ainsi de réduire l’impact carbone de la production horlogère suisse de manière très conséquente, puisque cet «acier solaire» divise les émissions carbones par 165.
«Nous avons déjà des pré-commandes sur cet acier de la part de marques horlogères, souligne Raphaël Broye. On ressent cet engouement, mais nous ne voulons pas y perdre notre âme: nous souhaitons avant tout encourager une nouvelle habitude de production locale, circulaire, avec une valorisation des déchets. Nous démontrons qu’il est possible de travailler avec des salaires suisses, de produire des petites quantités et de concurrencer des gros producteurs, même en Chine. Quand on sait que 80% du coût de production de l’acier est lié à l’achat d’énergie, la pérennité du modèle économique que nous mettons en place devient évidente.»
«Quand on sait que 80% du coût de production de l’acier est lié à l’achat d’énergie, la pérennité du modèle économique que nous mettons en place devient évidente.»
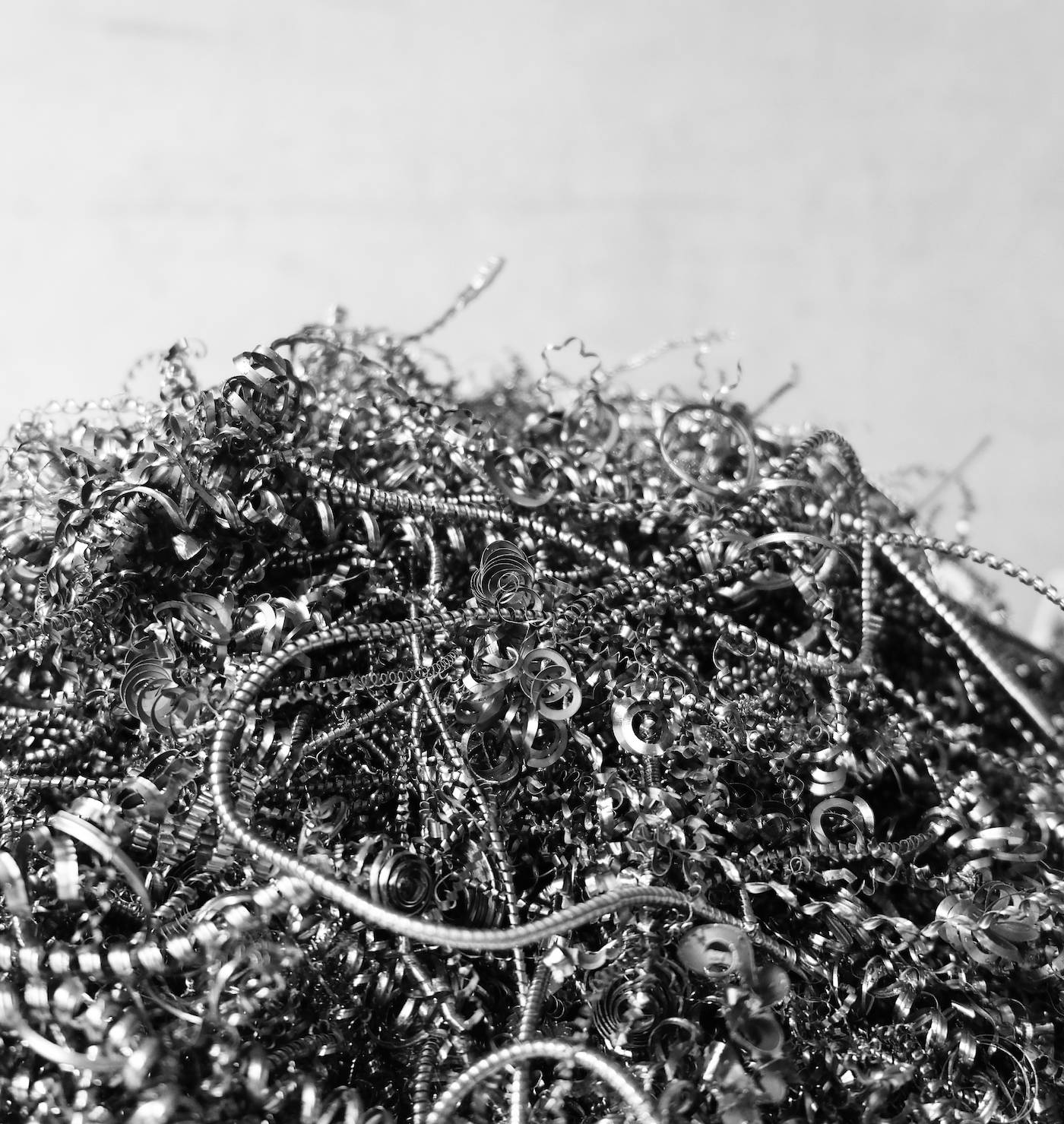
Au-delà de l’acier, du béton au vitrage recyclé
Le but à terme est de multiplier les fours proches des sources de déchets d’acier. Et le besoin est grand, comme le relève Raphaël Broye: «La Suisse importe 120’000 tonnes d’acier, toutes industries confondues… alors même qu’elle exporte 52’000 tonnes de copeaux ou déchets d’acier. Quel réservoir! Nous avons mis des GPS dans des containers de ces déchets d’aciers pour comprendre leur parcours une fois sortis de Suisse: ils ont parcourus près de 42’000 kilomètres avant d’être traités. On marche sur la tête! Il y a 600 PME rien que dans l’Arc jurassien, qui utilisent 15’000 tonnes d’acier. Demain, celles-ci pourraient être en totale auto-suffisance pour leurs approvisionnements.»
Panatere entre dans la phase de confirmation de la technologie et de la rentabilité de son modèle circulaire. «2023 sera l’année de la validation de ce modèle, puis nous passerons à la phase de duplication du système, annonce Raphaël Broye. Notre objectif stratégique à l’horizon 2025 est de créer la première usine industrielle auto-suffisante, non reliée au réseau électrique. Elle génèrera sa propre énergie et pourra atteindre des températures de fonte jusqu’à 2’000°C en ensoleillement optimal.» Mais ce n’est pas tout: «Nous sommes aussi en train de développer une palette complète d’applications grâce à des points de fusion complémentaires. Nous pourrons ainsi recycler du béton, des poutrelles métalliques, voire même du vitrage. Un deuxième four est en développement pour les métaux précieux.»
«La Suisse importe 120’000 tonnes d’acier, toutes industries confondues… alors même qu’elle exporte 52’000 tonnes de copeaux ou déchets d’acier. Quel réservoir!»
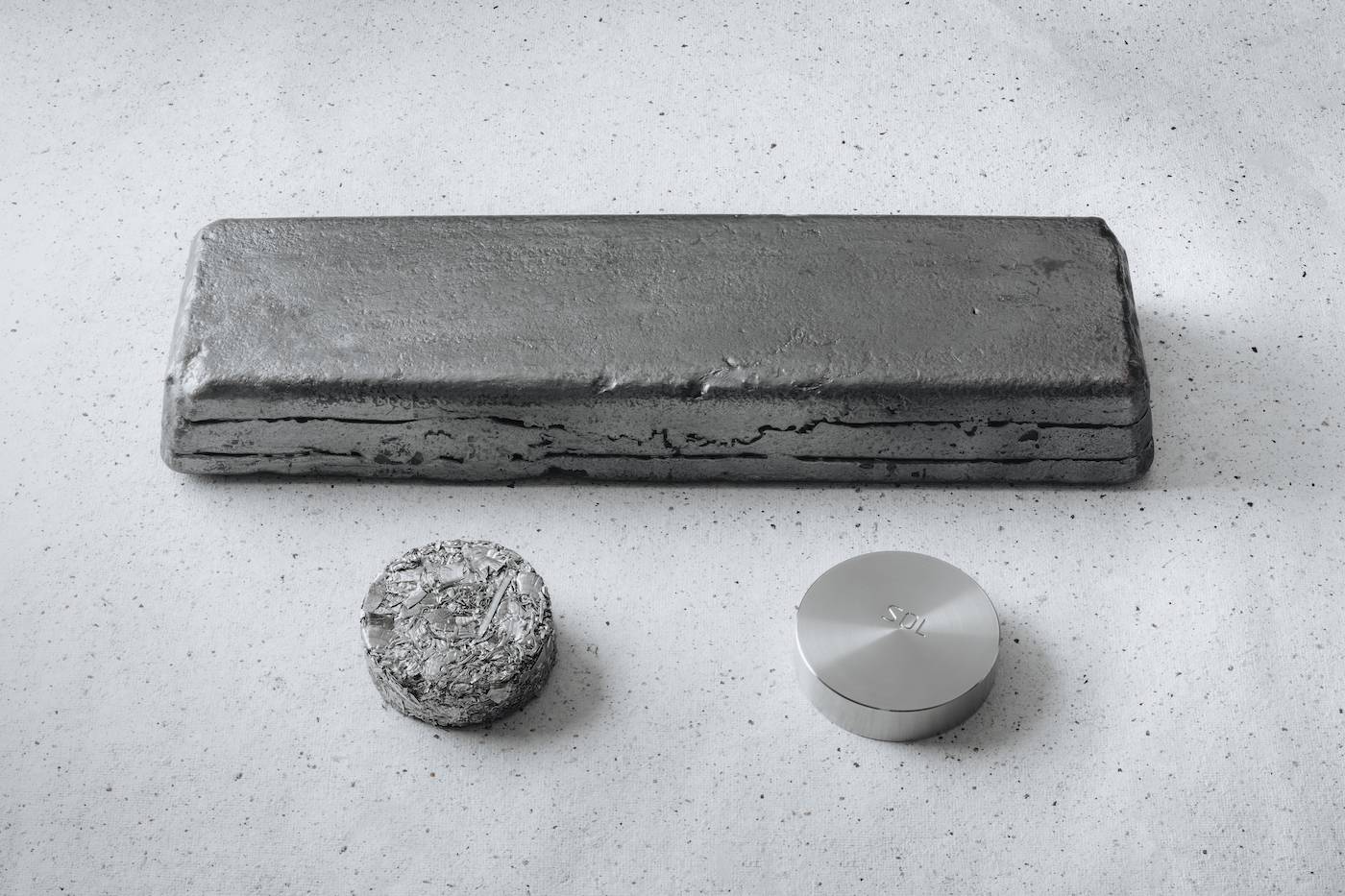
Montrer la valeur tangible du modèle circulaire
Autre projet de Panatere: la construction d’un immeuble totalement constitué d’éléments recyclés, des matériaux métallurgiques qui le composent jusqu’aux câbles électriques qui l’alimentent. «Nous avons déjà obtenu un substitut du cuivre deux fois moins cher que le matériau actuel et prévoyons d’en produire 2’000 tonnes uniquement à La Chaux-de-Fonds et Soleure, précise le responsable. Le titane est possible aussi, ainsi que l’or bien entendu ». Panatere ne compte pas s’arrêter aux métaux: l’entreprise peut aussi créer avec sa technologie des matériaux organiques, à base de lin, de fenouil ou encore de déchets de raisins – une kyrielle d’éco-matériaux qui ne manqueront pas d’intéresser l’industrie de la montre et du luxe.
«Notre objectif stratégique à l’horizon 2025 est de créer la première usine industrielle auto-suffisante, non reliée au réseau électrique. Elle génèrera sa propre énergie et pourra atteindre des températures de fonte jusqu’à 2’000°C en ensoleillement optimal.»
Si les autorités fédérales soutiennent ce projet d’usine vertueuse, Panatere entend rester indépendante à tout prix: « Nous appelons de nos vœux le fait d’être copiés, mais nous avons une éthique à préserver avant tout, souligne Raphaël Broye. Nous avons déposé des brevets pour nous protéger de prédateurs malveillants et cupides, mais nous sommes prêts à partager avec ceux qui le souhaitent… pour les bonnes raisons. Quand on voit que l’EPFL consacre 28% de son budget à la circularité, on se rend compte de l’importance du projet. L’économie circulaire va créer six fois plus d’emplois que la numérisation d’après l’école polytechnique. Ce n’est que le début.»
Panatere entend démontrer avec son four solaire qu’il est possible d’innover et de faire des affaires différemment, en mettant en place des processus qui ont du sens, à la fois rentables et positifs pour la planète. «Il faudrait que toute l’industrie se mette à trier ses déchets en amont – tout comme nous, citoyens, le faisons déjà à titre individuel», conclut Raphaël Broye. Panatere, en tout cas, semble bien faire sa part.