u bout du vallon du Locle, juste à côté des Moulins souterrains du Col-des-Roches, se trouve un bâtiment où l’on travaille la matière comme peu savent le faire dans l’industrie. Comadur, comme son nom l’indique (c’est l’acronyme de «Composants en Matériaux Durs»), est spécialisée dans le travail de composants à la dureté éprouvée, nécessitant un traitement particulièrement exigeant: cristaux synthétiques (saphir, rubis), céramiques, micro-composants... Cette entité de Swatch Group est l’un des secrets bien gardés qui permettent à l’horlogerie suisse de continuer à innover dans la recherche matériaux.
L’un de ses principaux clients à l’intérieur du groupe est Rado, dont la devise est justement «Master of Materials». Ce champion de la céramique haute technologie, introduite dès 1986 dans son modèle Integral (grâce, déjà, à la collaboration avec Comadur), produit des montres dont la texture peut faire penser à une deuxième peau, soyeuse, ultra-légère, inrayable, et dont la température s’adapte à celle du corps.
-
- La céramique est au centre des travaux de Rado depuis de nombreuses décennies, comme le montrent nos propres archives (un document de 1991).
- ©Europa Star Archives
Mais la fabrication de cette céramique haute technologie est loin d’être aisée, entre minutie dans le traitement des poudres de base et maîtrise des températures de cuisson d’une matière qui peut s’avérer capricieuse. Les racines de Comadur, qui emploie plus de mille employés sur sept sites de production en Suisse, remontent à la consolidation de l’industrie horlogère suite à la crise du quartz: la société est née en 1984 de la fusion des entreprises Seitz & Co, Méroz Pierres SA, Sadem SA et Watch Stones & Co SA, résultant elles-mêmes de différentes fusions successives. La plus ancienne, Méroz Pierres SA, s’était lancée en 1880 dans la fabrication de pierres d’horlogerie en rubis.
Cette entité de Swatch Group est l’un des secrets bien gardés qui permettent à l’horlogerie suisse de continuer à innover dans la recherche matériaux.
Un type de céramique peu commun
Pour la production de plusieurs millions de pièces en céramique (principalement des carrures, cadrans, lunettes et bracelets) qui sont fabriquées chaque année sur les sites de Comadur, tout commence par un procédé chimique: la société dose ses propres matériaux de base – en l’occurrence de l’oxyde de zirconium (ZrO2), sous forme de poudre. «La définition la plus large et élémentaire de la céramique, c’est un composé chimique non organique et non métallique qui durcit à la cuisson, souligne Oian Nicolas, CEO de Comadur. Elle est d’ailleurs très présente dans la vie de tous les jours, du carrelage à la poterie. Notre approche de ce procédé est cependant de haute technologie: nous utilisons de la poudre de zircone synthétique extrêmement pure et fine pour concevoir un matériau très dense, sans porosité, contrairement à la poterie qui n’est pas à 100% imperméable.»
Deux processus de fabrication principaux coexistent: le pressage, dans lequel la poudre est comprimée, ou l’injection, la méthode la plus courante pour les céramiques de Rado. Cette technique permet notamment de créer des formes plus complexes. A l’oxyde de zirconium sont ajoutés des pigments, résistants à de très hautes températures, afin de colorer la céramique, ainsi que des polymères (brevetés par Comadur) aidant à la mise en forme par injection. «Le processus de fabrication de nos céramiques est très délicat car aucune pollution, même minime, ne pourra être tolérée, précise Oian Nicolas. Par exemple, quelques traces de fer et la matière ressortira jaunâtre.»
-
- L’injection, la méthode la plus courante pour la production des céramiques de Rado
Il s’agit d’abord de définir comment la pièce pourra être fabriquée afin de respecter le design fixé par les marques. Avec une contrainte de taille: à la cuisson, la forme va perdre environ le quart de ses dimensions sous l’effet de la température – ce qu’il faut déjà bien intégrer dès la conception des moules d’injection. Des logiciels de simulation servent à tester les réactions des matériaux, afin de créer le moule le plus précis possible.
-
- Gravure laser
Une fois moulées, les pièces sont placées à l’intérieur d’un four et exposées durant plusieurs heures à une température extrêmement élevée (1’450 °C), un processus de frittage ayant pour effet de durcir la céramique, qui atteint sa couleur finale, alors que le polymère s’évapore. L’usinage de la pièce ainsi obtenue, à l’aide d’outils diamantés, permet de parvenir aux dimensions exactes. Suivent le polissage, en la plongeant dans un bain contenant des porteurs en céramique vibrant à haute fréquence; le sablage, qui donne une finition mate; la gravure laser des éventuelles inscriptions (tels les chiffres sur la lunette), qui sont ensuite laquées; enfin, le contrôle qualité.
A la cuisson, la forme va perdre environ le quart de ses dimensions sous l’effet de la température – ce qu’il faut déjà bien intégrer dès la conception des moules d’injection.
Alchimie contemporaine
Grâce aux travaux de Comadur, Rado a également pu introduire en 2019 de nouvelles céramiques colorées, à travers les modèles True Thinline Les CouleursTM Le Corbusier, allant d’un intense orange éclatant à un délicat Terre de Sienne pâle. Différents oxydes sont mélangés à la poudre de base pour obtenir les couleurs désirées, un subtil travail d’alchimiste contemporain. «En céramique, le noir est la couleur la plus simple à produire, paradoxalement bien davantage que le blanc, même si les composés chimiques paraissent blancs au début du processus», relève Oian Nicolas.
-
- Rado Captain Cook Chronograph
Une finition extraordinaire a également été introduite chez Rado – un effet découvert d’abord accidentellement il y a plus de deux décennies – le plasma, qui donne un aspect «métallique» à la céramique. Un effet particulièrement apprécié à l’ère du sport-chic, dans une industrie où la désirabilité des modèles acier domine. Comadur est l’une des très rares entités dans le monde à maîtriser cette technologie, qui voit l’oxyde de zirconium passer dans une enceinte dont la torche plasma peut atteindre les 20’000°C (gare aux yeux lors de la visite), ce qui permet de retirer les atomes d’oxygène. L’ajout de carbone donne lieu à la formation de carbure de zirconium – une autre céramique – dont l’aspect est proche de celui de l’acier, tout en conservant les avantages de la céramique: inrayable, légère, soyeuse, hypoallergénique, durable (contrairement à un revêtement PVD, par exemple). Et cela sans métal aucun.
-
- Comadur est l’une des très rares entités dans le monde à maîtriser la technologie plasma, qui voit l’oxyde de zirconium passer dans une enceinte dont la torche plasma peut atteindre les 20’000°C, ce qui permet de retirer les atomes d’oxygène.
Sous l’impulsion de Rado, Comadur a également développé d’autres céramiques comme le CeramosTM, un matériau composé de céramique haute technologie à 90% et d’alliage métallique à 10%. La société a en outre développé de la céramique haute technologie ultra-légère grâce au nitrure de silicium. Avec le temps, elle a aussi expérimenté différentes techniques de décoration sur sa céramique, que l’on retrouve à travers les marques de Swatch Group: croissance d’or, vernis, Liquidmetal, Super-Luminova®, incrustation de pierres précieuses...
Une finition extraordinaire a également été introduite chez Rado – un effet découvert d’abord accidentellement il y a plus de deux décennies – le plasma, qui donne un aspect «métallique» à la céramique.
Plusieurs millions de pièces en saphir
L’autre grande spécialité de Comadur est le travail du saphir synthétique. Plusieurs millions de pièces sortent de ses différents sites chaque année: une majorité de glaces, mais aussi des cadrans et des lunettes. La base est cette fois de l’oxyde d’aluminium: une flamme portée à 2’050°C, va faire fondre la poudre d’alumine, aboutissant ainsi, par solidification des gouttelettes créées, à un monocristal sous forme de cylindre – à l’instar d’une stalagmite.
Le résultat de cette opération, connue sous le nom de «procédé Verneuil», est un monocristallin de saphir synthétique, qu’il s’agit encore de stabiliser avant de le découper au fil diamant pour obtenir les rondelles de saphir qui donneront notamment lieu aux glaces protégeant le cadran de la montre. Au sein de son site de Bad Zurzach, Comadur déploie ainsi pas moins de 550 chalumeaux dédiés à cette opération industrielle!
Une autre méthode de production du saphir synthétique, qui a le mérite d’éviter toute perte de matière lors de la fabrication, est baptisée «EFG». Elle est notamment employée pour certaines glaces qui nécessitent des géométries, dimensions et épaisseurs particulières. Un creuset métallique, généralement réalisé en tungstène ou molybdène, contient un bain d’alumine fondue à partir duquel le cristal de saphir va être généré. Un germe est trempé à la surface du bain, entraînant ainsi une solidification locale, due à la différence de température entre le germe et le bain. Le cristal se forme ensuite par l’action d’un mouvement ascensionnel, permettant à la matière de se solidifier au fur et à mesure de la montée.
-
- Rado Captain Cook High-Tech Ceramic
Comadur réalise des monocristaux de saphir sous forme de plaques dont les dimensions peuvent atteindre 1,5 mètre de long pour 15 cm de large et plusieurs millimètres d’épaisseur. Mise en place en 2017, cette méthode a permis de recycler plusieurs années de matière saphir qui n’avait pas pu être utilisée. Ou comment le surplus d’un procédé devient la ressource d’un autre... Un recyclage de matière première qui s’inscrit dans la démarche de durabilité de Comadur et Swatch Group.
Les saphirs colorés sont quant à eux peu nombreux, à l’exception bien entendu du rubis, qui fait partie de la même famille de matériaux. Des machines CNC et des outillages spécifiques ont été mis au point avec des fournisseurs externes pour cette production complexe. Entre 40 et 70 opérations distinctes sont effectuées pour parvenir jusqu’à la glace qui équipera la montre. Là aussi, de nombreuses finitions sont disponibles: anti-reflet, effet «ghost», tactile (pour la T-Touch)... Comadur produit annuellement plus de 100 tonnes de saphir par procédé Verneuil et 25 tonnes de saphir par EFG.
Mise en place en 2017, la méthode EFG a permis de recycler plusieurs années de matière saphir qui n’avait pas pu être utilisée. Ou comment le surplus d’un procédé devient la ressource d’un autre...
La rencontre de l’énergie et de la matière
Du Locle, on parcourt ensuite les 60 kilomètres qui séparent Comadur du siège de Rado, juste à côté de Bienne. On y retrouve Adrian Bosshard, ancien champion suisse de moto et figure historique de Swatch Group: après avoir dirigé Certina pendant 17 ans, il a pris la tête de Rado en 2020. Ayant visité la production des céramiques qui équipent la majorité des montres de la marque, on comprend mieux que celle-ci se soit constitué «une communauté très loyale de clients», comme le souligne Adrian Bosshard. L’impression au poignet est si particulière qu’elle ne laissera personne indifférent: certains pourraient ne plus rien vouloir porter d’autre...
-
- Après avoir dirigé Certina pendant 17 ans, Adrian Bosshard a pris la tête de Rado en 2020.
Pour le responsable, c’est peut-être la Captain Cook High-Tech Ceramic lancée l’an dernier qui représente le mieux le cheminement de Rado, dans une époque fascinée par les modèles historiques: l’alliage d’un design datant de soixante ans exactement, répondant aux codes très en vogue de la «plongeuse», et d’une matière qui est le fruit de la technologie de pointe des ingénieurs du Locle, avec un côté très épuré et contemporain dans la sensation qu’elle livre. L’avantage de la céramique est en effet qu’elle ne vieillit pas – même si le design qu’elle incarne est lui-même «vintage». Une matière si particulière également qu’on ne saurait vraiment lui attribuer de genre, ce qui tombe bien dans une époque qui ne supporte plus ce type de catégorisation...
-
- Introduite cette année, la Captain Cook High-Tech Ceramic Diver est le fruit des dernières techniques de production de la céramique haute technologie. Elle se décline en six versions différentes (dont deux plasma).
Ce printemps, Rado a lancé une nouvelle Captain Cook Diver certifée ISO et équipé sa montre-phare de 1962 d’un chronographe. En cette année anniversaire pour cette collection, la marque a aussi dévoilé une édition limitée, la Captain Cook Over-Pole, une montre de 37 mm aux codes très vintage. Un lancement stratégique sur le deuxième semestre est la relance de la DiaStar Original, la montre pionnière anti-rayures, particulièrement reconnaissable à son boîtier de forme et qui est d’ailleurs née la même année que la Captain Cook. Modèle clé de Rado, la Diastar Original a été produite et vendue sans interruption par la marque pendant ces 60 dernières années, ce qui représente plus de cinq millions d’exemplaires fabriqués au cours de ces décennies.
-
- En 1962, Rado a dévoilé une montre inrayable pionnière: 60 ans plus tard, la DiaStar Original fait peau neuve. Un article de 1962 dans Europa Star.
- ©Europa Star Archives
L’innovation restera clé si Rado entend défendre son titre de Master of Materials à plus long terme: «Je viens du monde de la compétition sportive et j’ai bien appris que même si vous battez un record, un autre coureur finira par vous rattraper, souligne Adrian Bosshard. Il y a toujours de quoi se développer: le plasma ou la céramique de couleur le démontrent bien, tout comme le Nivachron résistant aux champs magnétiques qui équipe nos mouvements.»
«Il y a toujours de quoi se développer: le plasma ou la céramique de couleur le démontrent bien, tout comme le Nivachron résistant aux champs magnétiques qui équipe nos mouvements.»
-
- Lancée en 1962, la DiaStar Original emblématique de Rado connaît une renaissance à l’occasion de son 60ème anniversaire. Une édition spéciale a été imaginée par le designer Alfredo Häberli, surmontée d’une coiffe en Ceramos finement brossée. Le mouvement automatique Rado R764 garantit une réserve de marche de 80 heures.
La céramique reste le terrain de jeu bien particulier de Rado, que d’autres marques ont certes adopté mais pas dans les mêmes proportions. Cet axe bien défini signifie aussi que l’horloger s’écarte quelque peu des circuits d’approvisionnement traditionnels du secteur et peut revendiquer une maîtrise de son appareil de production. A condition bien sûr, de sécuriser son approvisionnement en matières de base, là où d’autres marques cumulent stocks d’or et d’acier. Et de traverser un hiver énergétique de tous les dangers pour des installations reposant sur des fours à très haute température. La rencontre de l’énergie et de la matière: ainsi pourrait-on qualifier le processus qui mène à la création si particulière des modèles de la marque...
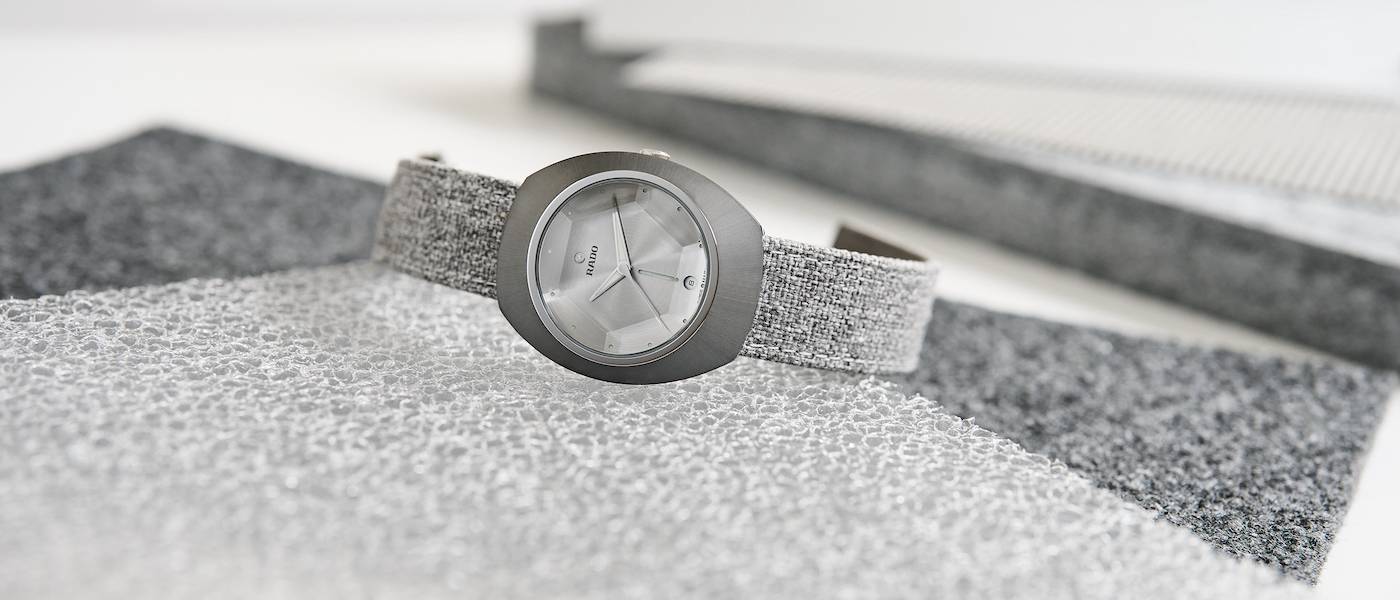
LES ÉTAPES DE PRODUCTION DES CÉRAMIQUES
-
- CONCEPTION DU MOULE - Un moule est créé à partir des plans du designer.
-
- MOULAGE PAR INJECTION - Le moule est placé au sein d’une machine où a lieu le moulage par injection.
-
- FRITTAGE - Les boîtiers sont placés à l’intérieur d’un four spécial, à une température extrêmement élevée (1’450°C). Durant de longues heures, la céramique se durcit et atteint sa couleur finale intense et sa dureté maximale, alors que le polymère s’évapore. Lors de ce procédé, le boîtier se rétracte d’environ 25% pour atteindre sa taille définitive.
-
- USINAGE - Les dimensions finales précises peuvent être usinées à l’aide d’outils diamantés afin d’atteindre l’exactitude nécessaire.
-
- POLISSAGE - Les composants destinés à avoir un éclat exceptionnel sont plongés dans un bain contenant de petits fragments de céramique vibrant à haute fréquence.
-
- SABLAGE - Un sablage de précision est réalisé pour obtenir une finition mate.
-
- GRAVURE - Un laser grave différents chiffres et marquages au niveau de la lunette avec des contours et une profondeur absolument parfaits.
-
- FOUR À PLASMA - Les composants destinés à la finition céramique haute technologie plasma subissent un autre traitement dans un four. La couleur blanche initiale est transformée en une nuance et une finition métallique permanentes.
-
- LAQUAGE - Les minuscules vides réalisés par le laser sont remplis d’une laque qui, une fois sèche, se fixe de façon permanente sur la céramique. Ce travail minutieux et délicat est réalisé par des horlogers.
-
- CONTRÔLE QUALITÉ - Une inspection rigoureuse est effectuée afin de s’assurer que le résultat final réponde aux standards de la marque.